How much of an advantage is your inventory giving you?
The decision to hold inventory in your business is not an easy one. It ties up cash and requires storage space and management. Even though holding inventory comes at a cost, the reward can be significant especially when it gives your business an edge over its competitors by adding value to your customer. The downside of holding inventory is when your business fails to see a return on this investment.
Holding inventory should give your business the following benefits:
The Inventory Cycle
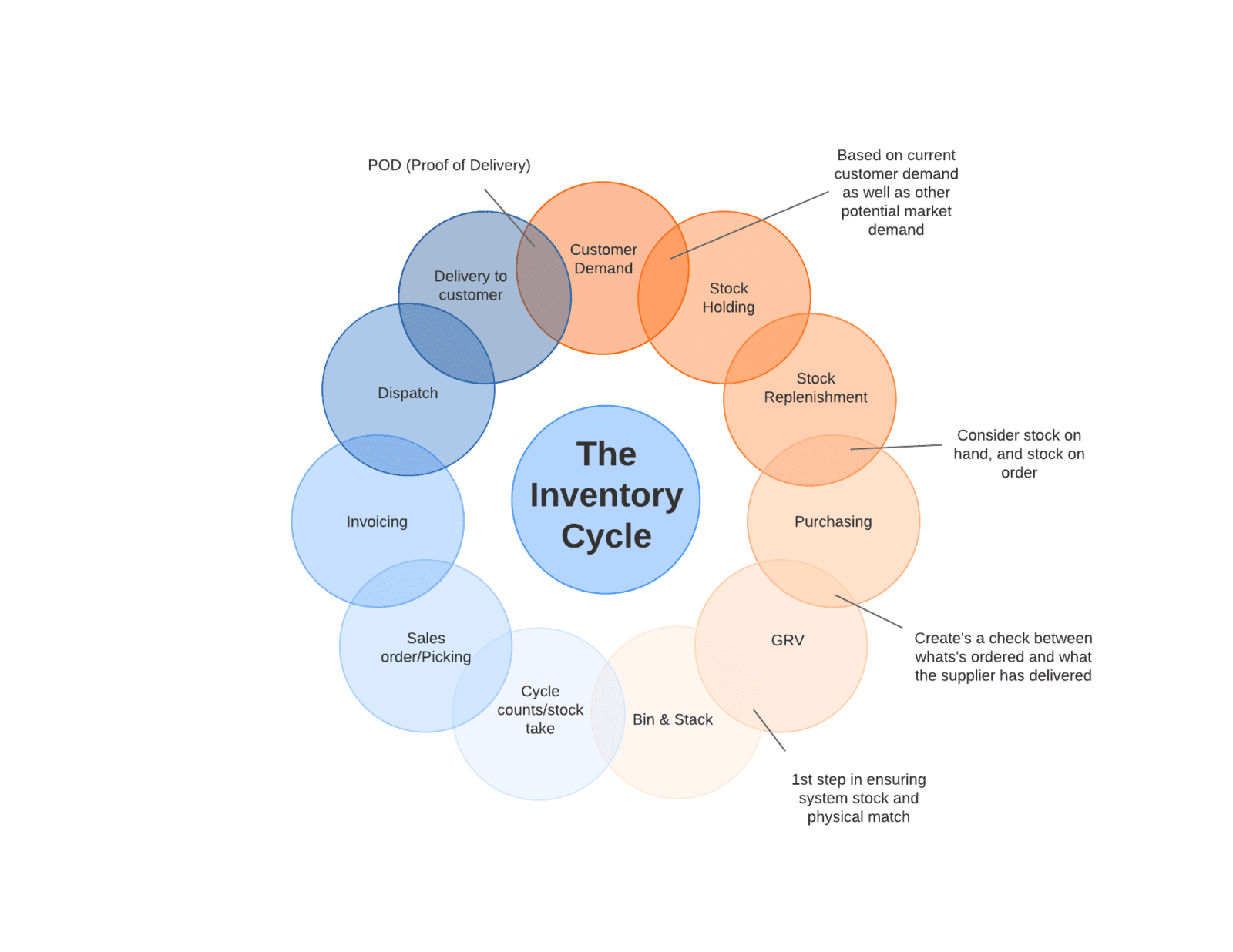
Customer Demand
Your business exists to satisfy a demand, essentially the problem you need to solve for your customer. The challenge here is quantifying this demand and then meeting it. Using a variation of techniques, you can get very close to always having stock, or having it available within a shorter time period
Stock Replenishment
Replenishing stock procedures can only happen once customer demand is understood, this of course is an ongoing process. You need to be able to adjusts as needed as the the environment is always changing. Replacing stock already used works best when the process is somewhat automated, and does not have to rely on manual calculations.
Purchasing
Purchasing as the name suggest is buying the needed stock from already vetted suppliers. At this point you should already have multiple suppliers on your database to call on to supply the required stock. As with the replenishment of stock, the purchasing function relies heavily on the accuracy of the stock records, and customer demand information
GRV of Items
A Goods Received Voucher (GRV) is a system term when you received the purchase stock into your inventory management system. This step should involve the physical inspection of the goods, quantity check against the PO and record of this stock on the system. This is a very important step as it notifies the rest of the company, these goods are on the premises and available for use
Packing and Binning
Part of the GRV process, this step is essential in ensuring the goods you ordered, received and paid for, that is needed for your customer demand is found when needed. Failure to complete this step with accuracy can lead to the items not being found when needed, exposes it to theft and leaves your customer unsatisfied.
Cycle Counts
The main purpose of a Cycle count is to regularly count specific fast moving items, to ensure that the physical inventory matches up to the theoretical (system) figures. These type of counts shortens the time between any possible discrepancies occurring and the company finding out, hence leaving a more manageable time period to investigate and fix.
Stock Take
Stock takes, unlike cycle counts, is when all the inventory in the business is counted. This helps the company get an accurate rand value of the stock being held on the premises. It's also an ideal opportunity to deal with variances, and slow moving (redundant) stock. Usage of stock must be prohibited during a stock take, essentially all movement of goods, in, out or within the company is not allowed.
Picking & Invoice
This part of the inventory cycle is made a whole lot easier if the GRV, packing and binning steps are done correctly. Picking needs to be done quickly and accurately. Customer satisfaction is highly reliant on delivering the right goods at the right quantity as per demand. Once the picking is done, the invoice can be generated ensuring the goods are off the system, and payment can happen
Dispatch
The final part of the inventory cycle, which done on time ensures a happy client, and repeat orders. This step involves issuing the goods that were invoiced to the driver, customer or collecting agent. A POD (proof of delivery) is generated once customer or agent acknowledges receipt of goods.
An over view from demand to supply
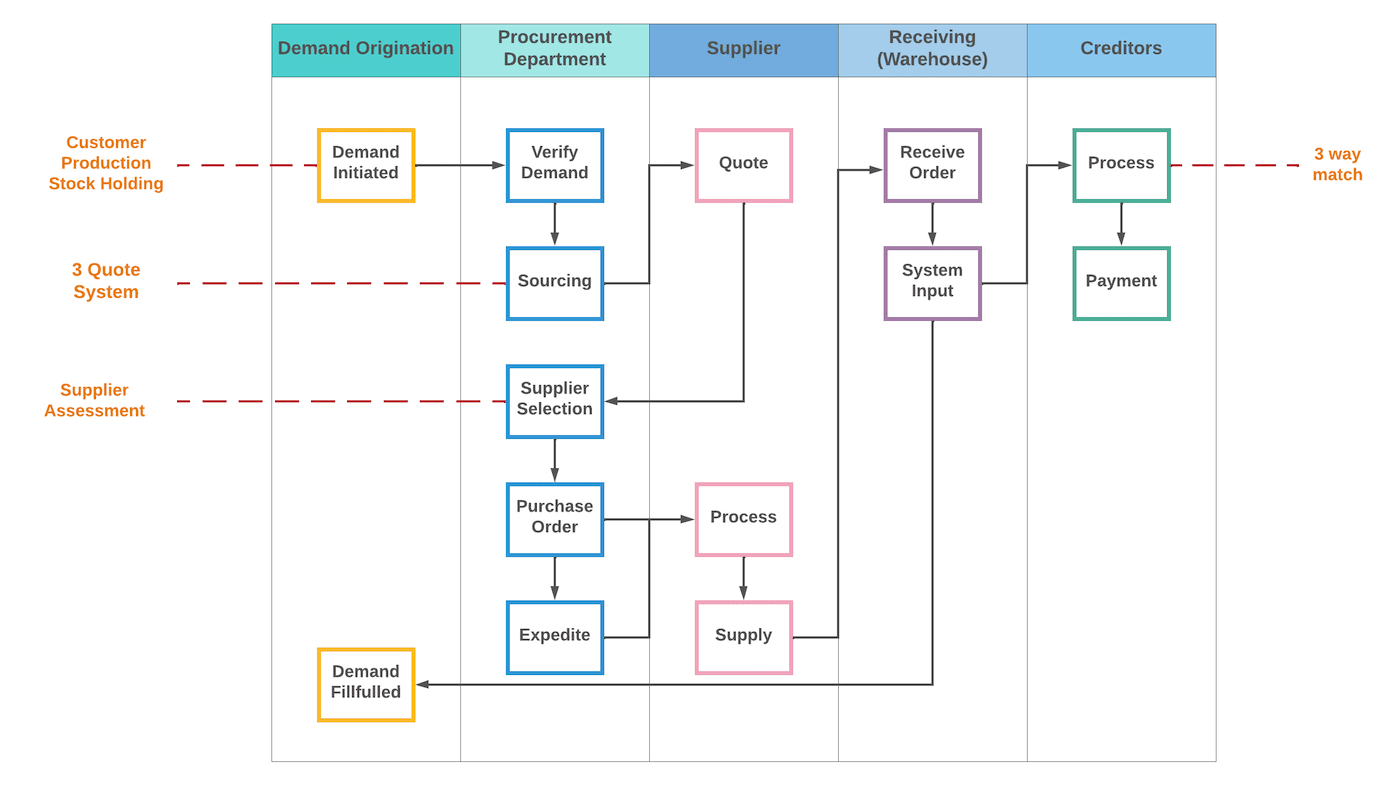
Our Solution
Detailed Services
With a very systematic approach we can get your Inventory Management System to where it needs to be. Why not get in touch with for a FREE
Consultation to address your challenges